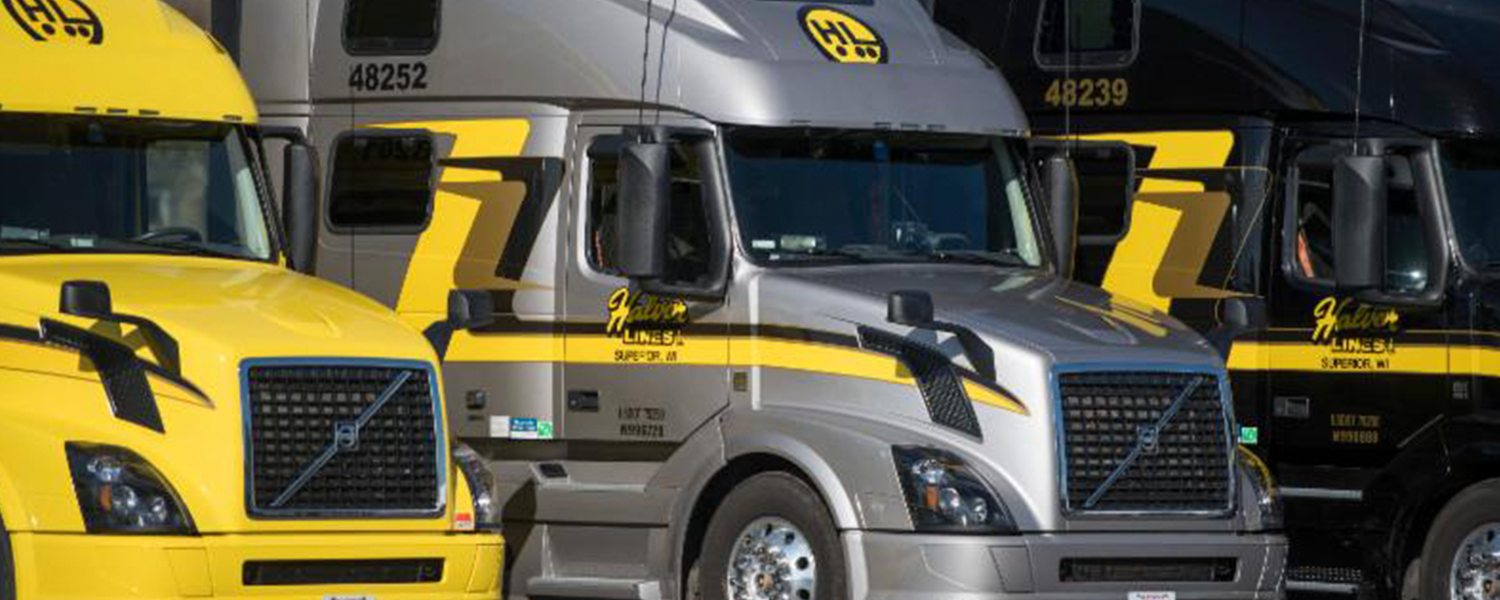
Halvor Lines Tunes Driver Training with CarriersEdge
As a carrier founded in 1968, Halvor Lines has quite a resume. It has an on-time delivery rate of 98 percent. It’s been named carrier of the year - twice - by United States Gypsum. It’s been a Best Fleet to Drive For®, for five consecutive years. It’s environmentally minded - having been selected by a major trade magazine of as one of the industry’s top 50 green fleets. And the fleet is safe - recognition has come from its home state of Wisconsin (first place in the more-than-5 million-mile category), along with first place in TCA’s National Fleet Safety Award for safety and security division.
According to Adam Lang, Halvor’s chief risk officer, those metrics have taken a lot of hard work and effort. “It’s accomplished by treating our customers right and having an open and honest relationship. And, it’s by living by our motto that our drivers are captains of their ships. If our drivers don’t feel safe in any situation - like in bad weather - our first response is ‘what would you like to do?’ Our first and foremost concern is for our drivers and their safety. So, if there is a delay in getting a shipment to a customer due to our driver-first mentality, we let the customer know what’s happening -- and they understand. That’s why it’s so important to have the open line of communication with our customers. This way we’re all working together.”
Based in Superior, Wisconsin, Halvor Lines operates 438 power units - mostly late model Volvo 780s with the average age less than 24 months. It runs a mix of flatbed, dry vans, and refrigerated units throughout the United States and Canada.
Its dedication to drivers is reflected in a turnover rate of just 38.5 percent. “We’re a Certified Top Pay Carrier with the NTI (National Transportation Institute),” said Lang. “And, we have low CSA scores thanks to our culture of safety and new equipment, plus a wellness program. We also have an engaged leadership team and an all-inclusive culture.”
Having safe, well-trained drivers is a key to success at Halvor. Lang said the company leaves no stone unturned with its safety efforts, which includes working with CarriersEdge. “We’ve evolved our training,” he said. “We’re working with CarriersEdge during new driver orientation, plus use their modules for continuing education as drivers continue on with us. It was a needed change of direction for our company. Before CarriersEdge, we were running up to five hours of safety and training videos during orientation, and while it checked off the box that drivers saw the video, they really didn’t absorb the content. It was easy for them to zone out while watching. Our orientation modules with CarriersEdge - which go over C-TPAT and Security and Threat Awareness, provide our drivers with information, along with tests that engage them. They retain the information. They learn.”
Those orientation modules dovetail with hands-on learning. Halvor has its own L3 truck simulator at its headquarters and new drivers typically drive the “low bridge simulation” to test their driving skill. “We also have continuing education with the simulator - having drivers come in once a year to test their skills against various driving scenarios,” said Lang.
While on the road, Lang said education continues. “Our safety team works with our drivers individually, and if they sense a need for training in one area, or sharpening a driver’s skill in another, they choose from CarriersEdge’s list of training modules. Our drivers like this method since they can use their laptop or tablet and do the module when it’s most convenient. And, we can monitor how our drivers are doing and record their progress. What’s more, our team really likes the functionality we have with CarriersEdge. We’re able to upload our own material. We’ve been using the Smith System on defensive driving -- all drivers are required to take this advanced defensive driving course conducted at our Superior and Inver Grove Heights terminals. It’s eight hours of paid training. The refresher courses are then taken on-line through the CarriersEdge portal.”
According to Lang, one of the modules from CarriersEdge even contributed to saving the day when a driver was hauling a load of turkeys recently. “A reefer ran out of fuel, and the driver couldn’t remember how to prime the motor to restart it, so he called his trainer,” said Lang. “Our trainer, Bob, was trying to verbalize how to do it, but then recalled that the CarriersEdge module on reefer operation actually went over the process. So, while on the phone, the trainer instructed the driver to use the CarrersEdge app on his phone, and look up the food safety module. He did, he followed the steps and got the motor started. That was big for us - the driver was in Texas and if he waited too long, we could have lost the load, which was valued close to $80,000.”
Lang said he’s a big fan of mobile training for drivers. “It’s efficient and the way CarriersEdge puts its training modules together, the drivers learn and are engaged. And, CarriersEdge is preferred by drivers. We had a new driver come in for orientation - he had been with four companies over the past 10 years. He asked about training, and we told him about our program with CarriersEdge. He let out a sigh of relief, and said, ‘that’s great, I was hoping I wouldn’t have to sit through a series of videos.’”
According to Lang, driver training today is a far cry from where the company was when he started at Halvor in 2012. “Back then we had our drivers come in three times a year for company-wide driver training and meetings on company progress. It slowed down productivity and the drivers weren’t always happy about having to spend the better part of a day at the terminal instead of putting miles on the trucks. It was also inefficient and costly for the company. We knew we had to do something different; something; something better. And, with CarriersEdge, coupled with our other programs, we are. Drivers learn better when they can choose their own learning environment.”